Saturday, 29 April 2017
Sunday, 9 April 2017
Cost Center & Work Center Integration!!
What is a Cost center in SAP?
SAP
cost center can be created for each
organization function or department to record the cost incurred which
contribute to a company’s profitability indirectly. Here some of the cost
center categories generally used in SAP
·
Production
·
Sales
·
Administration
·
Service Cost center
In SAP production
planning, each work
center will be assigned to one cost
center. For every activity type defined in a work center, an activity rate will
be maintained in the cost center. SAP system uses this information to calculate
activity cost for an operation.
We can assign a work center to only
one cost center. But we can assign several work centers to one cost center.
Example
Consider a cement making industry
where cement bulk are manufactured from Clinker, Gypsum, Fly Ash, Slag
(Granulated), Limestone etc. A Ball Mill operates on 120 T per day and the
following activities are performed in Ball Mill to make the Bulk cement:
1. Machine hours
2. Labor
hours
3. Setup
hours
In this case, we can define 3
activity types in the work center MILL-1 (Ball Mill - A) and assign them to
work center MILL-1. The work center is assigned to the cost center EX1_PQ_Production.
Activity rate for each activity (Machine hours, Setup hours and labor hours) are maintained against the cost center. Planned Machine hours, Setup hours and labor hours are maintained for the base quantity of 120 T (ball mill capacity) in a routing. Formula for each activity (Machine hours, Setup hours and labor hours) are maintained in a work center.
Activity rate for each activity (Machine hours, Setup hours and labor hours) are maintained against the cost center. Planned Machine hours, Setup hours and labor hours are maintained for the base quantity of 120 T (ball mill capacity) in a routing. Formula for each activity (Machine hours, Setup hours and labor hours) are maintained in a work center.
Activity
Cost Calculation Formula
When a production order is created
in the SAP system, it uses the above information to calculate the activity
cost.

Example of SAP Work Center and SAP
Cost Center Integration
Activity Types in Costing

Activity Types in SAP Cost Centers
Activity Price of Activity type
Activity price will be defined for
each activity type and cost center manually. In this example, even though we
have similar activity types for the cost center, activity price will be
different for the cost center. The activity price is defined in the
transaction KP26.
Activity Cost in Product Costing
In general, product cost in SAP
comprise of three primary components:
1.
Raw material or component cost
2.
Activity cost
3.
Overhead cost
Here, activity cost is calculated
based on work centers, cost centers and activity prices. The SAP system
calculates the activity cost by multiplying the activity price to quantity of
operations.
Example of Activity Cost in Product Costing
Let’s consider an example. A work
center ball mill produces bulk cement for 50 kg Cement Bag. This work center
has the following activities:
1.
Setup
2.
Machine
3.
Labor

SAP Work Center Assignment to SAP
Cost Center
The work center is assigned to the
cost center (3010255001) and each activity (setup, machine and labor) is assigned
with an activity type (MSUSFG, MACSFG and LABSFG).
Now, let’s look at activity price
calculation. Activity prices are maintained for the cost center (3010255001) and
activity types (MACSFG, MSUSFG and LABSFG) in the transaction KP26 by
a controlling person.



Labor Activity Price (Cost Center
3010255001 and Activity Type LABSFG)
Next, let’s check routing details of
the material. It will specify how many units of each activity are required for
manufacturing a base quantity of this material.

SAP Routing for a Material
(Transaction CA01)
Now lastly we perform a costing run
for the material in transaction CK11N to see how the SAP
system calculates product cost for this material.
The calculation is performed
according to the following formula:
Machine hour activity cost = Machine
activity price / Unit * Quantity from Formula
Subscribe to:
Posts (Atom)
Featured post
Introduction to manufacturing and non-manufacturing costs!!
A manufacturing company incurs both manufacturing costs (also called product costs) and non-manufacturing costs or expenses (also called ...
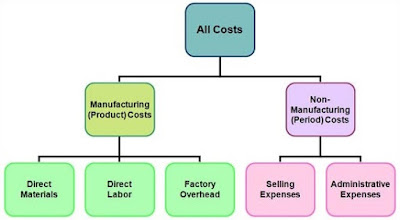
-
What is a Cost center in SAP? SAP cost center can be created for each organization function or department to record the cost incurred w...
-
During subcontracting, your company orders material from an external supplier. Unlike a normal external procurement process, your company ma...